COGS for a construction company includes all the direct and indirect costs associated with completing a construction project. These costs are used to determine the actual expenses incurred to produce the completed project, including direct labor, materials, and other related costs.
Calculating COGS for a construction company is more complex than for other industries. It requires a deep understanding of the industry and the unique challenges of project-based work. This article will provide you with a comprehensive understanding of COGS Construction, its significance, calculation methodology, and optimization strategies for effective cost management.
Key Takeaways
- COGS Construction includes all direct and indirect costs related to a construction project, impacting the bottom line and profitability of a construction company.
- Calculating COGS for the construction industry is more complex than for other industries due to project-based work and requires a deep understanding of the industry.
- Optimizing COGS is crucial for effective cost management and maximizing profitability.
What is cost of goods sold for construction company?
The concept of COGS, or Cost of Goods Sold, is a critical aspect of financial management for any construction company. COGS represents the direct costs associated with producing the goods or services sold by a company. In the case of construction companies, COGS includes all costs directly related to construction projects.
The construction industry has unique considerations when it comes to calculating COGS. Unlike other industries, such as manufacturing or retail, construction companies deal with complex projects that often involve multiple phases and many different costs. Therefore, accurately calculating COGS in the construction industry can be challenging but is essential for understanding the true cost of building projects.
“The construction industry is notorious for its complexity, and calculating COGS is no exception. Construction companies must carefully track all direct and indirect costs associated with each project to determine the true cost of construction.”
Industry | Average COGS Percentage |
---|---|
Construction | 55% |
Manufacturing | 60% |
Retail | 65% |
The table above shows the average COGS percentage for the construction, manufacturing, and retail industries, highlighting the relatively lower percentage for construction. This suggests that construction companies are generally more efficient in their operations and can achieve a lower COGS percentage compared to other industries.
Overall, understanding COGS is critical for any construction company to ensure that projects are profitable and that the business is financially sustainable. In the following sections, we will explore the direct and indirect costs that go into COGS for construction companies and the different methods used to calculate it.
Direct costs included in COGS Construction
In the construction industry, direct costs are expenses directly tied to a specific project or product. These costs are included in the calculation of COGS for a construction company. Direct costs can be broken down into three categories: materials, labor, and subcontractor costs.
Materials
Materials are the physical components used to construct a building or project. These can include items such as lumber, concrete, drywall, and electrical wiring. Materials are typically purchased from suppliers and delivered to the construction site. The cost of materials can vary widely depending on the type of project, the quantity of materials needed, and the current market conditions.
For example, the cost of lumber has seen significant fluctuations in recent years due to changes in supply and demand. In 2018, the cost of lumber reached an all-time high, with prices doubling from the previous year. This increase in material costs can have a significant impact on the bottom line for construction companies.
Labor
Labor costs include the wages, salaries, and benefits paid to workers who are directly involved in the construction process. This can include carpenters, electricians, plumbers, and other skilled tradespeople. Labor costs can also include the cost of supervisors and project managers who oversee the construction process.
The cost of labor can vary depending on a number of factors, including the location of the project, the skill level of the workers, and the duration of the project. For example, construction projects in urban areas may have higher labor costs due to higher wages and increased competition for skilled workers.
Subcontractor costs
Subcontractor costs are expenses incurred when a construction company hires another company or individual to work on a specific aspect of the project. This can include subcontractors for electrical work, plumbing, and HVAC systems. The cost of subcontractors can vary widely depending on the scope of work and the specific qualifications required.
For example, a construction company may hire a subcontractor who specializes in installing solar panels for a specific project. The cost of the subcontractor would be included in the calculation of COGS for that project.
Understanding the direct costs included in COGS Construction is crucial for construction companies. By accurately calculating and controlling these costs, construction companies can improve their profitability and overall financial performance.
Indirect Costs and Overhead Expenses
In addition to the direct costs included in COGS for construction companies, there are also indirect costs and overhead expenses that play a significant role in the overall calculation of COGS.
Indirect costs are expenses that are not directly tied to a specific project but still contribute to the construction process. These costs can include equipment maintenance, repairs and replacements, and general construction supplies.
Overhead expenses, on the other hand, are costs that are not directly related to the construction process but are necessary to run the business. These costs can include insurance, rent, utilities, and administrative salaries.
It is important to note that while these expenses are not directly tied to a specific project, they still impact the bottom line of the company and must be accounted for in the overall calculation of COGS. Neglecting to include these expenses can result in inaccurate financial reporting and poor decision-making.
Indirect Costs and Overhead Expenses Table
Indirect Costs | Overhead Expenses |
---|---|
Equipment maintenance | Insurance |
Repairs and replacements | Rent |
General construction supplies | Utilities |
“The inclusion of indirect costs and overhead expenses in COGS for construction companies is crucial for accurate financial reporting and decision-making. Ignoring these costs can result in poor business management and ultimately affect the profitability of the company.”
Exclusions from COGS Construction
While there are various types of costs that are included in COGS for a construction company, there are also some that are typically excluded. These exclusions can impact the accuracy of the COGS calculation, which is why it is important for construction companies to understand what should and shouldn’t be included.
One example of an exclusion from COGS is marketing expenses. While marketing is an integral part of promoting a construction company’s services and securing new projects, these costs are not directly tied to any particular project. Therefore, they are not typically included in COGS for a construction company.
Another example of an exclusion is interest payments. These expenses relate to financing activities and do not directly contribute to the cost of goods sold. As such, they are not included in the COGS calculation.
Finally, non-project-related expenses are also typically excluded from COGS. These may include things like rent, utilities, office supplies, and other overhead costs that are not directly tied to any specific project.
Why are these costs excluded?
The rationale behind excluding these costs from COGS is that they are not directly tied to the production process. COGS is designed to reflect the direct costs of producing goods or delivering services, not the general operating costs of a business. Therefore, including these costs in the COGS calculation could result in an inaccurate representation of the true cost of goods sold.

The exclusion of certain costs from the COGS calculation is essential for accurate financial reporting and effective cost management.
COGS Construction Calculation Methods
There are various methods to calculate COGS for a construction company, and each method has its advantages and disadvantages. Below are some of the most common ways that construction companies use to calculate their COGS.
Job Costing Method
The job costing method involves calculating the costs for each project separately. This method is useful because it provides detailed information about the costs of each project. However, it can be time-consuming to implement, and it may not be suitable for companies that have a large number of small projects.
Percentage of Completion Method
The percentage of completion method involves recognizing revenue and expenses based on the percentage of work completed on a project. This method is useful because it provides a more accurate representation of the project’s financial performance. However, it can be complicated to implement, especially when dealing with long-term projects.
Completed Contract Method
The completed contract method involves recognizing revenue and expenses only when a project is completed. This method is straightforward to implement and is suitable for short-term projects. However, it may not provide an accurate representation of a company’s financial performance if it has long-term projects that span multiple accounting periods.
It’s important for construction companies to choose a COGS calculation method that aligns with their needs and business model. Companies that operate on long-term projects may benefit from using the percentage of completion method, while those that work on short-term projects may prefer the completed contract method.
Importance of Accurate COGS Calculation for Construction Companies
For construction companies, accurately calculating Cost of Goods Sold (COGS) is crucial for effective financial management. Inaccurate COGS can lead to misjudged project bids, unanticipated costs, and even bankruptcy.
Accurate COGS calculation provides construction companies with a clear understanding of their project costs and contributes to better decision-making processes. It also helps companies to identify inefficiencies and cost-saving opportunities, ultimately improving the bottom line.
By tracking and analyzing COGS data, construction companies can monitor their financial performance and make informed decisions. This enables construction companies to optimize their financial performance and remain competitive in the industry.
Moreover, accurate COGS calculation is particularly important for construction companies that work on government contracts. The government uses COGS to verify the accuracy of a contractor’s pricing proposals and can reject a proposal if it is deemed unreasonable due to an inaccurate COGS calculation.
In conclusion, accurate COGS calculation is essential for construction companies to make informed decisions, manage costs efficiently, and maintain profitability. By leveraging the right tools and metrics, construction companies can optimize their COGS and ensure long-term success.
Impact of COGS Construction on profitability
One of the most significant financial metrics impacted by COGS Construction is profitability. A construction company’s bottom line is directly related to the accuracy of its COGS calculations. (COGS Construction)
When COGS is too high, it reduces the gross profit margin, which is calculated as the difference between revenue and COGS. A lower gross profit margin leads to a lower net profit margin, which is the profit remaining after all expenses have been paid. (profitability)
For example, a construction company with revenue of $1 million and COGS of $700,000 would have a gross profit margin of 30%. If the company’s COGS were to increase to $800,000, the gross profit margin would decrease to 20%, resulting in a lower net profit margin. (COGS Construction, profitability)
On the other hand, if a construction company can optimize its COGS by reducing direct costs and overhead expenses, it can increase its profit margins and improve its overall financial performance. By monitoring and analyzing COGS data regularly, construction companies can identify areas for improvement and implement strategies to maximize profitability. (COGS Construction, profitability)
Example:
Year | Revenue | COGS | Gross Profit Margin | Net Profit Margin |
---|---|---|---|---|
Year 1 | $1,000,000 | $700,000 | 30% | 10% |
Year 2 | $1,200,000 | $750,000 | 37.5% | 15% |
Year 3 | $1,500,000 | $800,000 | 46.7% | 20% |
In this table, we can see the impact of optimizing COGS on a construction company’s profitability over three years. In Year 1, the company has a gross profit margin of 30% and a net profit margin of 10%. By reducing COGS and increasing revenue, the company is able to improve its gross profit margin to 46.7% and net profit margin to 20% in Year 3. (COGS Construction, profitability)
Strategies for Optimizing COGS Construction
Construction companies can take several steps to optimize their COGS, maximizing profitability and improving financial performance. Below are some strategies that construction companies can implement:
- 1. Streamline operations: Reducing waste, eliminating inefficiencies, and optimizing processes can all lead to reduced direct and indirect costs, ultimately contributing to lower COGS.
- 2. Negotiate with suppliers: Engaging suppliers and subcontractors in cost negotiations can lead to better deals, lower material and labor costs, and ultimately, lower COGS.
- 3. Invest in technology: Implementing technology solutions such as construction management software and project tracking tools can improve efficiency and reduce redundancies, thereby lowering costs and optimizing COGS.
- 4. Optimize workforce: Hiring skilled labor, training staff, and improving employee efficiency can lead to reduced labor costs and overall cost savings, ultimately impacting COGS.
- 5. Monitor and track COGS: Regularly monitoring and analyzing COGS data can provide insights into cost trends, help identify areas of improvement, and ultimately contribute to optimized COGS and improved financial performance.
By implementing these strategies, construction companies can optimize their COGS and improve their bottom line, ensuring long-term financial sustainability and profitability.
Industry Benchmarks for COGS Construction
When it comes to COGS Construction, industry benchmarks can serve as a useful metric for construction companies to evaluate their financial performance against industry standards. By comparing their COGS to the average percentages established by the sector, construction companies can analyze their strengths and weaknesses and identify areas for improvement. Here are some industry benchmarks for COGS Construction:
Benchmark | Percentage (%) |
---|---|
Average COGS | 75-80% |
Gross profit margin | 10-20% |
Net profit margin | 2-6% |
As shown in the table above, the average COGS for the construction industry is between 75-80%. This figure includes all the direct and indirect costs associated with a construction project. The gross profit margin, which is the difference between the revenue and COGS, is typically between 10-20%, while the net profit margin, which accounts for all other expenses, is between 2-6%. These benchmarks can vary depending on the location and type of construction project, but they provide a general understanding of performance standards within the industry.
Construction companies should aim to keep their COGS within these benchmarks to remain competitive and profitable. By analyzing their COGS data and comparing it to industry standards, construction companies can make informed decisions regarding cost control and project management to optimize their financial performance.
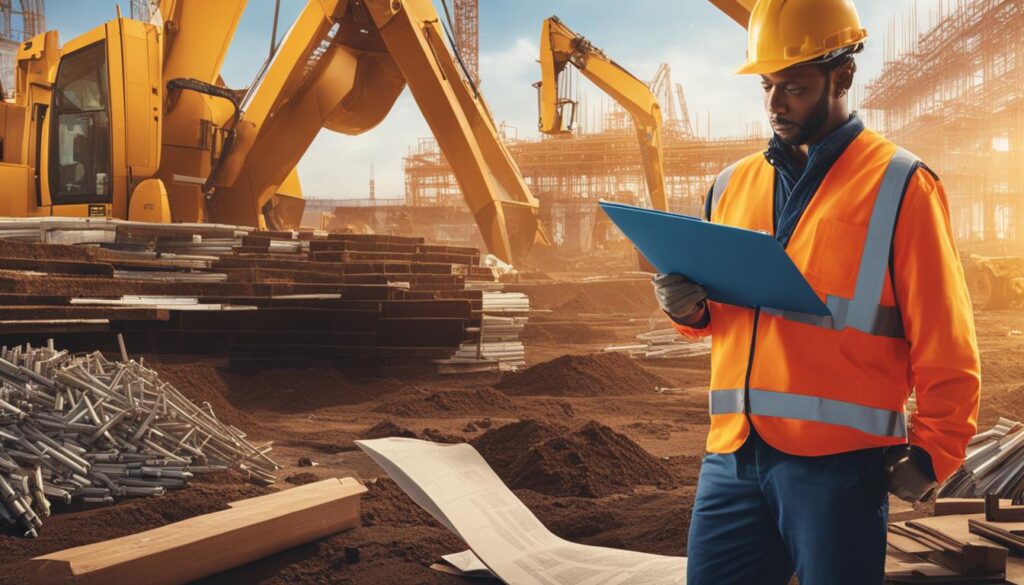
Tracking and analyzing COGS Construction data
Tracking and analyzing COGS Construction data is crucial for construction companies to monitor their financial health and make informed decisions. By regularly tracking and analyzing COGS data, companies can identify areas for cost control and operational efficiency improvements.
One effective way to track COGS data is to implement a comprehensive project management system that allows for accurate tracking of direct and indirect costs across projects. This system should also provide real-time updates on project status and expenses, enabling companies to quickly identify any cost overruns or inefficiencies.
In addition to project management systems, construction companies can use various software tools and metrics for analyzing COGS data. These may include financial modeling software, job costing metrics, and profitability analyses. By using these tools, companies can gain insights into their financial performance, identify key drivers of profitability, and benchmark their performance against industry standards.
COGS analysis metrics
Metric | Description |
---|---|
Direct material costs | Total material costs directly associated with a project or service. |
Direct labor costs | Total labor costs directly associated with a project or service. |
Subcontractor costs | Costs paid to subcontractors for work performed on a project. |
Overhead costs | Indirect costs associated with running a business, such as rent, utilities, and insurance. |
Gross profit margin | The percentage of revenue remaining after the cost of goods sold has been deducted. |
Net profit margin | The percentage of revenue remaining after all expenses, including COGS, have been deducted. |
By tracking and analyzing COGS data using these metrics, construction companies can gain a deeper understanding of their financial performance and identify areas for improvement. This can help companies make more informed decisions and ultimately improve their bottom line.
What are some facts about cost of goods sold in construction industry?
- Steel, concrete, and timber are primary elements in the cost of goods sold in the construction industry.
- Skilled labor wages form a significant part of construction COGS.
- Major factors in the cost of goods sold in construction include electrical and plumbing subcontracting.
- Outside of construction COGS, heavy machinery depreciation is a notable overhead expense.
- Variations exist between residential and commercial construction regarding the cost of goods sold.
- Client specifications heavily influence custom construction project COGS.
- Fluctuations in lumber and steel prices impact the cost of goods sold in the construction industry.
- Regional differences in labor and material costs affect construction COGS.
- Implementing advanced technologies can reduce the cost of goods sold in construction.
- Economies of scale are critical in lowering material costs in large-scale construction COGS.
- Seasonal weather conditions can potentially escalate the cost of goods sold in the construction industry.
- Economic booms typically result in a rise in construction COGS due to increased resource demand.
- Construction COGS can increase due to the costs of complying with regulatory standards.
- International material procurement and exchange rates influence the cost of goods sold in construction.
- Just-in-time inventory strategies are effective in reducing material holding costs within construction COGS.
- Workforce experience plays a crucial role in influencing labor costs in the cost of goods sold in construction.
- The use of sustainable materials can lead to higher construction COGS.
- Separate from construction COGS, insurance and bonding costs are additional financial considerations.
- Post-construction warranty expenses, though important, are not part of the initial cost of goods sold in the construction industry.
- Long-term maintenance and repair costs are typically excluded from the calculation of construction COGS.
Conclusion
Understanding COGS Construction is crucial for any construction company looking to optimize its financial performance. By gaining insights into the costs included in COGS, the calculation methods, and the impact on profitability, construction companies can make informed decisions and take steps to control costs and maximize profits.
Tracking and Analyzing COGS Construction Data
One of the key takeaways from this article is the importance of tracking and analyzing COGS data. Construction companies should have robust systems in place to collect and analyze data related to COGS on an ongoing basis. This will enable them to identify areas of inefficiency and take corrective action, as well as make informed decisions about resource allocation and project selection.
Optimizing COGS Construction
Another important aspect of COGS Construction is optimization. Construction companies should explore various strategies and best practices to control costs, improve efficiency, and maximize profitability. This may include negotiating better prices with suppliers, improving project planning and management, and investing in technology and equipment that can help streamline operations and reduce costs.
Industry Benchmarks for COGS Construction
It is also helpful for construction companies to have a benchmark against which to compare their COGS performance. Industry benchmarks such as average COGS percentages and key performance indicators can provide valuable insights and help companies identify areas for improvement.
Overall, by understanding and optimizing COGS Construction, construction companies can improve their bottom line and achieve greater financial stability and success.
FAQ
What is COGS for a construction company?
COGS stands for Cost of Goods Sold and refers to the direct costs incurred by a construction company in the production of its goods or services. It includes expenses such as materials, labor, and subcontractor costs.
How does COGS impact the financial performance of a construction company?
COGS has a direct impact on the bottom line of a construction company. By accurately calculating and controlling COGS, a construction company can determine its gross profit and net profit margins, which ultimately affect its overall financial performance.
What is the difference between COGS in the construction industry and other industries?
COGS in the construction industry includes specific costs associated with the construction process, such as materials and labor. Other industries may have different cost components depending on the nature of their goods or services.
What are the direct costs included in COGS for a construction company?
Direct costs included in COGS for a construction company typically encompass materials, labor, subcontractor costs, equipment rentals, and other expenses directly related to the construction process.
What about the indirect costs and overhead expenses in COGS Construction?
Indirect costs and overhead expenses in COGS Construction refer to expenses that are not directly tied to a specific project but still impact the overall cost of goods sold. Examples include equipment maintenance, insurance, administrative costs, and utilities.
Are there any costs excluded from COGS for a construction company?
Yes, certain costs are typically excluded from COGS for a construction company. These may include marketing expenses, interest payments, income taxes, and non-project-related expenses. The rationale behind the exclusion is that these costs are not directly tied to the production of goods or services.
What methods can construction companies use to calculate COGS?
Construction companies can use various methods to calculate COGS, such as the specific identification method, the weighted average cost method, and the first-in, first-out (FIFO) method. Each method has its own advantages and considerations.
Why is accurate COGS calculation important for a construction company?
Accurate COGS calculation is crucial for a construction company as it provides insights into the profitability and financial health of the business. It helps in decision-making, cost control, and resource allocation, leading to improved financial management.
How does COGS Construction impact profitability?
COGS Construction directly impacts profitability by affecting the gross profit margin and net profit margin. By effectively managing and optimizing COGS, a construction company can improve its profitability and overall financial performance.
Are there any strategies to optimize COGS Construction?
Yes, there are strategies that construction companies can implement to optimize their COGS. These include cost control measures, improving operational efficiency, leveraging technology, and implementing effective project management practices.
What are some industry benchmarks for COGS Construction?
Industry benchmarks for COGS Construction can provide a reference point for construction companies to assess their performance. Average COGS percentages and key performance indicators (KPIs) specific to the construction sector can help companies evaluate their efficiency and profitability against industry standards.
How can construction companies track and analyze COGS Construction data?
Construction companies can track and analyze COGS Construction data using specialized accounting software or project management tools. By monitoring key metrics and regularly analyzing the data, companies can gain insights into their cost structure and make informed decisions for ongoing performance evaluation.