Construction projects are often complex and involve multiple stakeholders, tight deadlines, and numerous challenges. One of the most significant problems that construction managers face is cost overruns. Cost overruns occur when the actual expenses exceed the originally estimated costs, resulting in budgetary shortfalls, delays, and other negative consequences. In this article, we’ll explore the most common causes of cost overruns in construction projects.
Key Takeaways
- Cost overruns are a common and serious problem in construction projects
- Construction managers need to identify the root causes of cost overruns to prevent them
- Inaccurate initial cost estimation, scope changes, project delays, unforeseen site conditions, poor project management, design errors, inefficient resource allocation, market fluctuations, supply chain issues, contractual disputes, legal issues, and lack of contingency planning are the most common causes of cost overruns
- Effective risk management, contingency planning, and solid project management practices can help mitigate the risk of cost overruns
Inaccurate Initial Cost Estimation
One of the primary causes of cost overruns in construction projects is inaccurate initial cost estimation. Budgeting errors can occur due to a variety of factors, such as underestimating project complexity, overlooking the cost of necessary materials, or failing to account for unforeseen expenses. These mistakes can lead to project costs exceeding the budget, causing delays and potentially compromising the project outcome.
The consequences of inaccurate cost estimation can be severe, with some studies suggesting that up to 85% of construction projects experience cost overruns. These overruns can have a ripple effect on the entire project, impacting everything from resource allocation to timelines and ultimately affecting the project’s bottom line. In some extreme cases, inaccurate budgeting can even result in project failure.
Common Budgeting Errors in Construction Projects
Some common mistakes made during initial cost estimation in construction projects include:
Mistake | Description |
---|---|
Not including all necessary materials and labor costs | Failure to account for all materials and labor costs can cause significant budget gaps when expenses begin to add up. |
Underestimating project complexity | Projects that are more complex than anticipated can result in significant delays and increased costs. |
Ignoring the cost of unexpected expenses | Unforeseen expenses can arise during the construction process, and failure to budget for these costs can result in significant overruns. |
Failure to account for market fluctuations | Changes in the price of materials can have a dramatic impact on the budget of a construction project. |
By identifying and addressing these budgeting errors early on, construction project managers can take steps to mitigate the risk of cost overruns and ensure the project stays on track.
Inaccurate initial cost estimation
One of the most significant causes of cost overruns in construction projects is inaccurate initial cost estimation. The budgeting errors made during the early stages of a project can have a considerable impact on its outcome. Inaccurate cost estimation can often result in unexpected expenses and delays, causing the project to go over budget and miss deadlines.
Common mistakes made during the budgeting process include underestimating labor costs, not accounting for the cost of materials accurately, and failing to include overhead expenses in the budget. Inaccurate cost estimation can also lead to inadequate funding for the project, causing it to be underfunded and requiring additional funding to complete.
Inaccurate cost estimation can have significant consequences on construction timelines. It can cause delays, resulting in extended construction periods and unnecessary increased expenses. Additionally, the need to renegotiate contracts and adjust construction deadlines can cause additional complications and expenses for the project.
Effective management of the budgeting process can prevent inaccurate cost estimation. The use of reliable data, previous cost estimates, and cost-benefit analysis can ensure the accuracy of the budget. Additionally, contingency planning can allow for adjustments in the budget when unforeseen costs arise, ensuring the project stays within budget and timelines.
Impact of Inaccurate Cost Estimation on Project Timelines
Impact | Description |
---|---|
Delays | Inaccurate cost estimation can lead to delays in the project, resulting in additional expenses and missed deadlines. |
Contract renegotiations | Renegotiations of contracts can cause additional expenses and delays in the project timeline. |
Extended construction period | Unanticipated expenses caused by inaccurate cost estimation can extend the construction period and cause additional expenses for the project. |
Inefficient resource allocation
One of the most common causes of cost overruns in construction projects is inefficient resource allocation. Poor management of materials, labor, and equipment can lead to unexpected expenses and delays, impacting the project timeline and budget.
Effective resource allocation requires careful planning and monitoring throughout the project. The project manager must ensure that the necessary resources are available when needed and that they are being used efficiently. This includes:
- Proper inventory management to avoid shortages or excess materials
- Effective scheduling of labor to avoid over or under-staffing
- Regular maintenance of equipment to prevent breakdowns and delays
Failure to manage resources properly can result in increased costs, from the need to order additional materials, hire extra personnel, or replace damaged equipment. It can also lead to project delays and missed deadlines, which can cause further financial losses.
Efficient resource allocation is crucial to the success of any construction project. By carefully managing resources and ensuring that they are being used effectively, project managers can minimize the risk of cost overruns and keep projects on track.
Poor Project Management
Effective project management is crucial to ensuring that construction projects stay on budget and on schedule. However, ineffective leadership, lack of communication, and inadequate decision-making can all contribute to cost overruns.
One common issue is a lack of coordination between different teams and departments. For example, delays in obtaining necessary permits or approvals can cause construction to stagnate, resulting in additional costs. Inadequate supervision of subcontractors and suppliers can also lead to inefficiencies and unexpected expenses.
Another problem is poor communication between team members. When one part of the team is unaware of changes or issues encountered by another, it can lead to delays and unanticipated costs.
Finally, decision-making can be a major issue. When project managers fail to make timely decisions, it can cause construction to stagnate, leading to additional costs. In addition, decisions that are not fully thought through or based on incomplete information can lead to costly mistakes.
In summary, poor project management can result in cost overruns due to a lack of coordination, communication, and decision-making. Effective leadership and communication are key elements of successful project management, and project managers should prioritize open communication, timely decision-making, and close coordination with all team members.
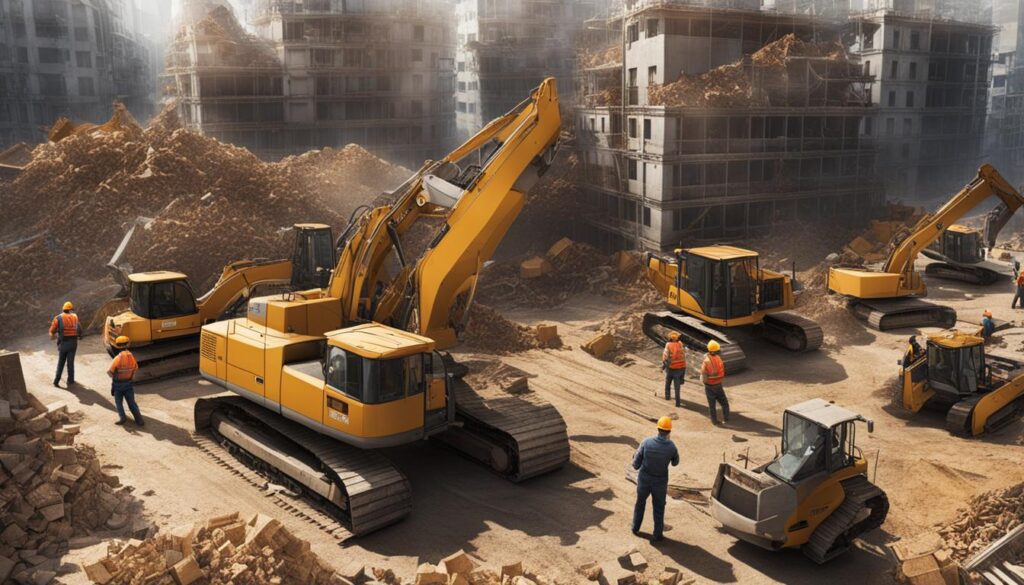
Inefficient Resource Allocation can be a result of Design Errors and Omissions
Efficient resource allocation is key to keeping construction projects within the budget. However, when design errors and omissions occur, it can lead to improper management of construction resources, causing delays and cost overruns.
For example, if the construction plans do not accurately reflect the necessary materials or equipment needed for a project, it can result in wasted resources or the need for additional purchases. This problem can further exacerbate if a construction project experiences design changes.
Consequently, it is vital to communicate effectively with the design team and ensure that all construction plans are thorough and accurate. This approach is particularly critical in complex projects with many stakeholders and contractors who need to manage their resources more carefully.
Additionally, proper allocation of resources includes managing labor and ensuring that each worker is appropriately trained and has the necessary skills to complete their respective tasks. Design flaws that lead to confusion or require additional training for workers can delay a project’s timeline and increase costs.
Therefore, it is crucial to prioritize clear communication between contractors, designers, and workers to mitigate the risks of inefficient resource allocation due to design errors and omissions.
Inefficient Resource Allocation in Construction Projects
Proper resource allocation is crucial to ensure the success of a construction project. However, inefficient management of materials, labor, and equipment can lead to unexpected expenses and delays that result in cost overruns. In this section, we will explore the impact of inefficient resource allocation and share some best practices to manage construction resources effectively.
Materials Management
One of the biggest challenges in resource allocation is managing construction materials. In many cases, ordering too much or too little of a material can incur additional costs. For instance, ordering excess materials can result in storage and handling expenses, while ordering too little can lead to delays and reordering fees. A lack of communication between project stakeholders can also cause inefficiencies in material management.
To prevent these issues, project managers can establish clear communication channels with suppliers and contractors to ensure that materials are delivered on time and in the correct quantity. They can also track material usage, forecast requirements, and eliminate waste by reusing or recycling materials whenever possible.
Labor Management
Labor costs are another significant expense in construction projects. Inefficient labor management can lead to low productivity, delays, and safety hazards. Poor communication, inadequate training, and lack of supervision can all contribute to ineffective management of construction labor. Additionally, inadequate staffing levels can stretch existing resources too thin, leading to additional expenses and delays.
To manage construction labor effectively, project managers should identify the required skill sets and staff levels for each project activity. They must establish standard operating procedures for each task and provide appropriate training to ensure that labor is used efficiently. Additionally, regular communication with workers, providing necessary resources and creating a positive work environment can stimulate productivity and increase job satisfaction.
Equipment Management
The use of equipment is also an important resource in construction projects. Inefficient equipment management may cause idleness, maintenance issues, or inadequate capacity in the equipment fleet. Subsequently, equipment-related expenses can start to add up, affecting the overall project budget. Furthermore, underutilized equipment can create safety issues for workers on the construction site.
To ensure efficient equipment management, project managers should schedule use of the equipment effectively and optimize the equipment fleet, focusing on equipment utilization. By identifying equipment needs upfront, rental expenses can be reduced, and the use of equipment can be strategically planned to maximize productivity.
Inefficient resource allocation can have a detrimental impact on construction projects, leading to increased expenses, delays, and safety hazards. However, by taking proactive steps to manage construction resources efficiently, project managers can mitigate these risks. By establishing clear communication channels, identifying resource needs upfront, and providing adequate training, construction projects can be completed within budget and on time.
Inefficient Resource Allocation: How It Contributes to Cost Overruns in Construction Projects
Construction projects involve a wide range of resources, including labor, materials, and equipment. Inefficient allocation of these resources can lead to unexpected expenses and delays, ultimately resulting in cost overruns. Let’s take a closer look at how inefficient resource allocation can impact construction projects and the strategies that can be implemented to prevent it.
Market Fluctuations
Market fluctuations can have a significant impact on the cost of construction materials. Changes in supply and demand, tariffs, and other economic factors can cause prices to rise or fall unexpectedly. This can make it difficult to accurately estimate the cost of materials and result in cost overruns if the budget is not adjusted accordingly.
To prevent this, project managers can implement strategies such as bulk purchasing, where materials are bought in large quantities at a fixed price, or hedging, where the price of materials is fixed through futures contracts. Another option is to create contingency plans that account for potential changes in material costs, providing a buffer against unexpected expenses.
Supply Chain Issues
Construction projects rely on a complex network of suppliers, manufacturers, distributors, and contractors. Any disruptions or delays in the supply chain can have a ripple effect on the entire project, causing delays and cost overruns. For example, a delay in the delivery of key materials can result in additional labor costs and missed project deadlines.
Effective supply chain management is crucial to prevent these issues. Project managers can establish strong relationships with suppliers and create contingency plans that account for potential supply chain disruptions. This can include identifying alternative suppliers, stockpiling critical materials, and creating backup plans for labor and equipment in case of delays.
Efficient resource allocation is key to the success of any construction project. By anticipating potential challenges related to market fluctuations and supply chain issues, project managers can implement strategies that prevent cost overruns and keep the project on track.
Contractual Disputes and Legal Issues:
Contractual disputes and legal issues can be a significant cause of cost overruns in construction projects. Disputes may arise from various factors such as miscommunication, conflicting interests, and a lack of clarity in the terms of the contract. These disputes can lead to delays, legal fees, and even project termination. The financial and time impact of these disputes can be detrimental to both the contractor and the client.
Construction contracts are legal documents that set out the responsibilities, rights, and obligations of the parties involved in the project. It is crucial to ensure that all parties have a thorough understanding of the contract and its terms before signing. However, even with a well-drafted contract, disputes may arise.
Common causes of contractual disputes include changes in project scope, delays, payment issues, and design flaws. Dispute resolution methods can include negotiation, mediation, arbitration, or litigation. Each approach has its advantages and disadvantages, and the choice of method will depend on the specific circumstances of the dispute.
Legal issues can also arise from non-compliance with local or state regulations, permits, or environmental requirements. Failure to obtain necessary approvals can result in legal action, fines, and project delays, adding to the project’s overall cost.
To avoid contractual disputes and legal issues, it is crucial to have clear communication, thorough documentation and follow the project plan. It is also recommended to engage legal experts to advise on contracts and to ensure that regulatory requirements are met.
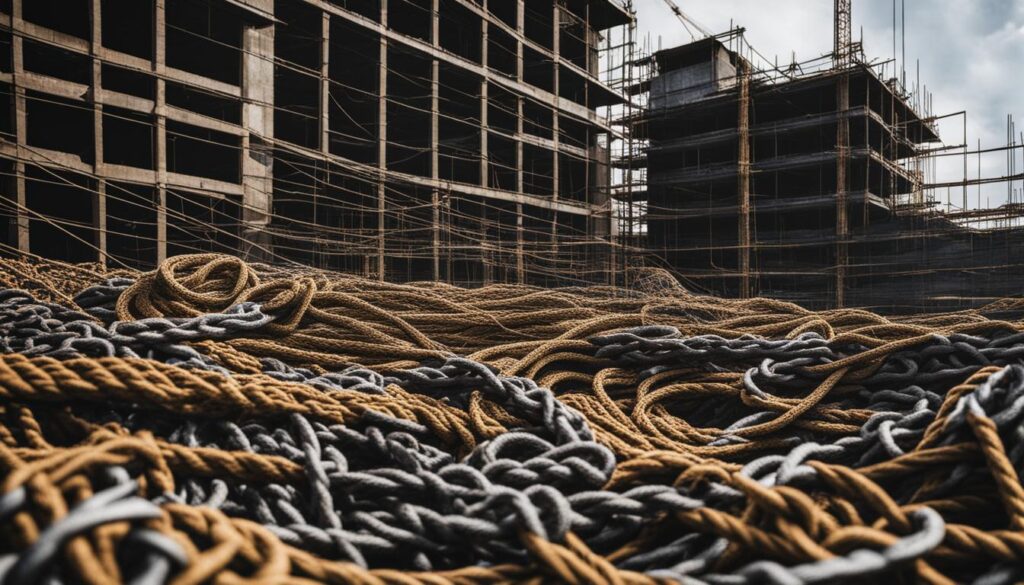
Lack of project contingency planning
A significant cause of cost overruns in construction projects is a lack of project contingency planning. Risk management is a critical aspect of project management that often gets overlooked, resulting in unexpected expenses that can have a detrimental impact on project timelines and finances.
Contingency planning involves identifying potential risks before they occur and preparing strategies to manage them effectively. This process can help keep projects on track and ensure that unexpected expenses are minimized.
One of the primary ways to approach contingency planning is by conducting a thorough risk analysis early on in the project planning process. By identifying potential risks and estimating their impact, project managers can develop mitigation strategies that can help reduce the likelihood of these risks occurring or minimize their impact if they do.
Another critical aspect of contingency planning is budget reserves. A project contingency budget is a separate amount of money set aside for unexpected costs. This budget is an essential component of any construction project and should be established before the onset of the project to prepare for unexpected expenses that may arise.
When a contingency budget is not established, project managers may be forced to divert funds from other areas of the project, resulting in an imbalanced distribution of resources. As a result, this can lead to cost overruns and project delays.
Effective risk management and contingency planning are vital components of any successful construction project. They help to ensure that potential risks are identified and managed before they become significant issues and provide a safety net for unexpected expenses. By investing time and resources into contingency planning, project managers can help avoid costly mistakes and deliver successful projects that come in on time and on budget.
Conclusion
In conclusion, cost overruns are a major challenge faced by construction projects. The causes of cost overruns are varied and can have significant impacts on project finances and timelines. It is crucial to identify these causes and take proactive measures to prevent them.
Effective initial cost estimation, managing scope changes and project delays, accounting for unforeseen site conditions, efficient resource allocation, and proper project contingency planning are some of the strategies that can help prevent cost overruns.
It is also important to have effective project management and leadership to ensure timely and efficient decision-making throughout the project. Thorough and accurate construction plans and designs can help prevent design errors and omissions. Additionally, being aware of market fluctuations and disruptions in the supply chain is crucial.
Risk Management for Successful Project Outcomes
Ultimately, successful project outcomes require a combination of effective risk management strategies. These include identifying and prioritizing risks, developing mitigation plans, and monitoring and controlling risks throughout the project lifecycle.
By taking proactive measures to address the root causes of cost overruns, construction projects can be completed on schedule and within budget, resulting in successful outcomes for all stakeholders involved.
FAQ
What are the most common causes of cost overruns in construction projects?
The most common causes of cost overruns in construction projects include inaccurate initial cost estimation, scope changes and project delays, unforeseen site conditions, poor project management, design errors and omissions, inefficient resource allocation, market fluctuations and supply chain issues, contractual disputes and legal issues, and lack of project contingency planning.
How does inaccurate initial cost estimation contribute to cost overruns?
Inaccurate initial cost estimation can lead to cost overruns by underestimating project expenses. Budgeting errors and miscalculations can result in inadequate funds being allocated, causing financial strain as the project progresses.
What impact do scope changes and project delays have on cost overruns?
Scope changes and project delays can cause cost overruns by disrupting the planned timeline and increasing project expenses. Unforeseen modifications and delays can result in additional labor, material, and equipment costs, as well as contractual penalties for timeline extensions.
How do unforeseen site conditions contribute to cost overruns?
Unforeseen site conditions, such as encountering unexpected geological, environmental, or structural challenges, can lead to cost overruns. Dealing with these unforeseen complications often requires additional resources, such as specialized equipment or expert contractors, resulting in increased project costs.
What role does poor project management play in cost overruns?
Poor project management, characterized by ineffective leadership, lack of communication, and inadequate decision-making, can contribute to cost overruns. Mismanagement of resources, failure to address issues promptly, and improper coordination can lead to delays, rework, and budget overages.
How do design errors and omissions impact cost overruns?
Design errors and omissions can contribute to cost overruns by requiring rework or modifications during construction. Incomplete or flawed construction plans can lead to delays, material wastage, and additional expenses to rectify the design issues.
How does inefficient resource allocation contribute to cost overruns?
Inefficient resource allocation, such as mismanaging materials, labor, and equipment, can lead to unexpected expenses and project delays. Lack of proper planning and coordination can result in wasted resources, increased labor costs, and downtime due to equipment unavailability.
How do market fluctuations and supply chain issues cause cost overruns?
Market fluctuations, such as volatile material prices, and disruptions in the supply chain can lead to cost overruns. Unanticipated price increases or scarcity of construction materials can significantly impact project budgets, requiring adjustments or alternative sourcing at higher costs.
How do contractual disputes and legal issues contribute to cost overruns?
Contractual disputes and legal issues can cause cost overruns by leading to delays, disputes, and breaches of contract. Resolving these issues can require legal intervention, additional negotiations, or compensation, resulting in increased expenses and project timeline extensions.
How does lack of project contingency planning impact cost overruns?
Lack of project contingency planning can contribute to cost overruns by failing to account for unforeseen expenses or risks. Without proper risk assessment and mitigation strategies, unexpected challenges can deplete project budgets, leading to delays and financial strain.