Construction projects are complex and require significant investment. From design and architectural expenses to labor and equipment costs, the financial aspects of construction are numerous. However, identifying the major expense in the construction industry is critical to understanding the financial complexities involved in construction projects.
In the United States, construction expenses have been rising steadily in recent years. According to the U.S. Census Bureau, construction spending in 2022 reached $1.4 trillion, a 4.7% increase from the previous year.
So, what is the biggest expense in construction?
The answer is not straightforward. The cost of construction projects varies depending on factors such as project size, location, and scope. However, certain expenses consistently rank as major contributors to overall construction costs.
Over the course of this article, we will explore the various expenses involved in construction projects, with a focus on identifying the biggest expense in the industry.
Key Takeaways
- Identifying the major expense in construction is critical to understanding the financial complexities of construction projects in the United States.
- Construction expenses in the United States have been rising steadily in recent years.
- The biggest expense in construction varies depending on project factors, but certain expenses consistently rank as major contributors to overall construction costs.
Understanding Construction Costs
Before delving into the specific expenses associated with construction projects, it is essential to understand the overall cost breakdown of the industry. Construction costs can be divided into three major categories:
- Materials
- Labor
- Overhead and administrative costs
These categories include all the expenses related to building and completing a construction project. When creating a cost estimate, it is essential to break down each expense into these categories to have a detailed understanding of the project’s financial requirements.
Much of the expense in construction projects goes towards materials. The specific materials used in a project will vary depending on its scope, but generally include:
- Lumber and other wood products
- Concrete and masonry
- Steel and metal products
- Plumbing, electrical, and HVAC systems
- Roofing and insulation
The cost of materials can vary widely based on factors such as demand, availability, and location. For example, a project in a rural area may have higher material costs due to transportation expenses.
Labor costs are also a significant expense in construction projects. This includes the cost of hiring construction workers, as well as any subcontractors or specialized labor required for the project.
Finally, overhead and administrative costs include expenses such as project management, office operations, insurance, and legal fees.
Cost Breakdown Example
“This cost breakdown example shows how the total project cost of $5,000,000 is divided between the three major categories of materials, labor, and overhead and administrative costs.”
Understanding the cost breakdown of a construction project is essential for developing an accurate budget and managing expenses effectively. By breaking down the costs into specific categories, project managers can identify areas where cost savings can be achieved and make informed decisions to keep the project on track financially.
Materials: A Significant Investment
When it comes to construction costs, materials are one of the most significant expenses. In fact, according to Construction Dive, materials account for about 40% of construction costs in the United States. Understanding material costs and procurement is therefore essential for effective project budgeting and financial management.
The cost of materials can vary widely depending on factors such as the type of material, the quantity needed, and the location of the construction project. For example, materials like steel and lumber have experienced significant price increases due to supply chain disruptions and high demand in recent years.
To manage material costs effectively, construction companies must engage in strategic procurement practices. This includes carefully selecting suppliers, negotiating prices, and tracking inventory to ensure efficient use of materials. Some companies may also consider alternative materials or methods of construction to reduce costs.
Importance of Material Procurement
Effective material procurement is not only important for managing costs, but it can also impact project timelines and quality. Delayed or incorrect delivery of materials can slow down construction, leading to additional expenses and potential hazards on the job site.
Construction companies must also consider factors such as the sustainability and environmental impact of materials. Using sustainable materials can not only reduce costs over time but can also boost a company’s reputation and appeal to environmentally conscious clients.
Comparison of Material Costs
Material Type | Average Cost Per Unit | Variability in Cost |
---|---|---|
Steel | $700 per ton | High |
Lumber | $500 per thousand board feet | High |
Cement | $100 per cubic yard | Low |
As shown in the table above, the cost of materials can vary significantly by type, with steel and lumber among the most expensive options. By carefully tracking costs and engaging in strategic procurement practices, construction companies can effectively manage material expenses and increase the likelihood of project success.
Labor: The Backbone of Construction Expenses
When it comes to construction expenses, labor costs are often the largest contributor. The construction workforce is essential to completing projects, and their wages, benefits, and productivity significantly impact the overall expense.
One of the biggest challenges facing the industry is the shortage of skilled labor. According to a survey conducted by the Associated General Contractors of America, 80% of construction firms report having difficulty filling hourly craft positions. This shortage can drive up wages and increase project timelines, leading to higher expenses.
In addition to wages, benefits such as healthcare, retirement plans, and paid time off also contribute to construction workforce expenses. It’s important to consider these costs when estimating project expenses and budgeting accordingly.
Expense | Cost Range |
---|---|
Hourly wages | $15-$80 |
Healthcare benefits | $5,000-$20,000 per employee per year |
Retirement plans | $3,000-$10,000 per employee per year |
Paid time off | $2,000-$6,000 per employee per year |
Improving productivity can also help reduce construction workforce expenses. Adopting new technologies, providing proper training, and improving communication between workers can all help increase efficiency and decrease project timelines.
Ultimately, understanding and managing labor costs is crucial for contractors and project managers to achieve success in the construction industry. By keeping track of wages, benefits, and productivity, and addressing issues such as the skilled labor shortage, construction companies can optimize their expenses and remain competitive in the market.
Equipment and Machinery Costs
Construction equipment expenses can significantly impact a construction project’s budget. The cost of purchasing and maintaining equipment can add up quickly. However, renting equipment might be a more cost-effective option for short-term projects. Rental fees are generally lower than the purchase price, and maintenance costs are usually included in the rental agreement.
Equipment maintenance is a crucial factor to consider in construction project budgets. The cost of repairing or replacing worn-out equipment can be significant, affecting the project’s timeline and budget. Regular maintenance can help prevent equipment breakdowns and increase productivity on the job site.
Advancements in technology have also impacted equipment expenses in construction. Newer equipment models often come with higher price tags but can improve efficiency and productivity on the job site. Therefore, it is essential to weigh the costs and benefits of purchasing or renting newer equipment models.
Comparing Equipment Purchase and Rental Costs
Cost Category | Purchase | Rental |
---|---|---|
Upfront Cost | High | Low |
Maintenance Cost | High | Included in the rental agreement |
Flexibility | Low | High – Equipment can be rented as needed |
Depreciation | Equipment depreciates over time, reducing its resale value | No depreciation, as equipment is rented |
It is advisable to evaluate the costs and benefits of purchasing or renting equipment to ensure the construction project stays within budget. Renting equipment might be more suitable for short-term projects, while purchasing equipment might be more feasible for long-term projects.

Equipment and machinery costs are among the most significant expenses in construction. Proper equipment maintenance, technological advancements, and cost-effective procurement strategies can help control expenses and keep construction projects within budget.
Permits, Inspections, and Compliance Expenses
Obtaining permits and complying with regulations are unavoidable expenses in the construction industry. Permits are required to ensure that construction projects meet safety and legal standards, and failure to comply can result in fines, delays, or even stop-work orders. Therefore, it is important to consider these costs when budgeting for a project.
The cost of construction permits varies widely depending on the location, type of project and the required permits. Building permits typically include fees for plan reviews, inspections, and issuance. Other permits, such as electrical or plumbing permits, may also be required, and each comes with its fees and costs.
In addition to permit fees, regulatory compliance costs are also significant. The construction industry is subject to various federal, state, and local regulations that govern workplace safety, environmental protection, and more. These regulations can lead to additional costs for training, monitoring, and reporting, depending on the project scope and location.
Inspections are also an essential part of compliance with regulations. Inspections are conducted by government inspectors or third-party inspectors and are designed to ensure that the construction project meets safety and regulatory standards. Inspections often require a fee, and multiple inspections may be needed at different stages of a project.
In summary, permit and compliance-related expenses can represent a significant portion of construction costs. It is crucial to factor these expenses into project budgets and timelines to avoid unexpected delays and expenses that can impact the overall success of a project.
“Compliance isn’t the only cost of doing business, it’s the cost of staying in business.” – Joseph Colihan
Overhead and Administrative Costs in the Construction Industry
Construction projects entail numerous expenses, including material costs, labor expenses, design fees, and the costs of obtaining permits and complying with regulations. However, the overhead and administrative costs of construction projects are often just as significant and can impact the overall expense of a project. This section will delve into the various types of overhead and administrative expenses typically associated with construction projects, including project management costs, office expenses, and insurance fees.
Project Management Costs
One of the most significant overhead expenses in construction is project management costs. These costs can include salaries for project managers and support staff, as well as expenses related to planning, scheduling, and monitoring the project’s progress. The industry has seen a rise in the use of project management software and other technologies, which can increase efficiency but also come with additional costs.
Office and Administrative Expenses
In addition to project management costs, construction projects also incur overhead expenses for office and administrative functions. These expenses can include rent, utilities, supplies, and equipment for the office. They can also include fees for legal and accounting services, as well as expenses related to marketing and advertising the company. Overall, these costs can add up quickly and impact the profitability of a project.
Insurance Fees
Construction projects also require insurance to protect against risks such as property damage, liability, and workers’ compensation. The cost of insurance varies depending on the size and scope of the project, as well as the level of risk involved. Insurance fees can be a significant overhead cost, particularly for larger projects.
“While overhead and administrative costs in construction may seem like a necessary evil, companies can mitigate these costs by carefully managing expenses and exploring technology solutions that increase efficiency.”
In conclusion, overhead and administrative costs represent a significant expense for construction projects, along with material costs, labor expenses, and other fees. Companies must carefully manage these expenses to maximize profitability and minimize risk. The next section will explore the expenses associated with design and architecture in construction.
Design and Architectural Expenses
One of the significant expenses in construction is architectural design costs. Architects play a crucial role in ensuring that buildings are structurally sound, aesthetically pleasing, and functional.
Construction drawings are essential in providing detailed plans and specifications for builders to follow. The cost of creating construction drawings varies based on the project’s size and complexity. A simple project may cost a few thousand dollars, while a larger and more complex one may cost tens of thousands of dollars.
Design consultants may also be necessary for specialized areas, such as electrical or mechanical engineering. The cost of hiring design consultants can vary, with some charging an hourly rate, while others charge a flat fee.
Overall, architectural design costs and construction drawings can significantly impact the project’s total expenses. However, it is essential to invest in quality design to ensure the building meets both aesthetic and functional requirements.
“Good buildings come from good people, and all problems are solved by good design.” – Stephen Gardiner
Financing and Interest Costs
Construction projects require significant upfront investment, and funding options are crucial to their success. It is common for construction projects to involve loans, whether from banks, credit unions, or other financial institutions. However, securing financing can come with additional costs beyond the loan itself, including interest expenses and loan fees.
Interest expenses can vary depending on factors such as the loan amount, interest rate, and loan term. Construction loans may have higher interest rates compared to traditional home loans, making interest expense a significant factor in overall construction costs. Borrowers should carefully consider the loan terms and interest rates before committing to any financing options.
In addition to interest expenses, there may be loan fees associated with securing financing. These fees can include origination fees, appraisal fees, and other related costs. It is essential to factor in these fees when determining the overall cost of financing a construction project.
One financing option for construction projects is a construction-to-permanent loan, which provides funding for both the construction phase and the permanent mortgage. This type of loan can simplify the financing process and potentially save borrowers money on closing costs and other fees.
Breaking Down the Costs
When financing a construction project, it is essential to understand how expenses will be broken down. The funds are typically disbursed in stages, with payments made directly to contractors and suppliers as the work progresses. This process is known as draws, and the number of draws can vary depending on the length of the project.
During the construction phase, interest payments are usually made on the amount of funding that has been disbursed, rather than the full loan amount. This means that interest expenses will increase as more funds are drawn, which can significantly impact the overall cost of financing.
Once the construction phase is complete, the loan is converted into a permanent mortgage, with the remaining balance due. Borrowers should be aware of any fees associated with this process and plan accordingly to avoid any surprises.
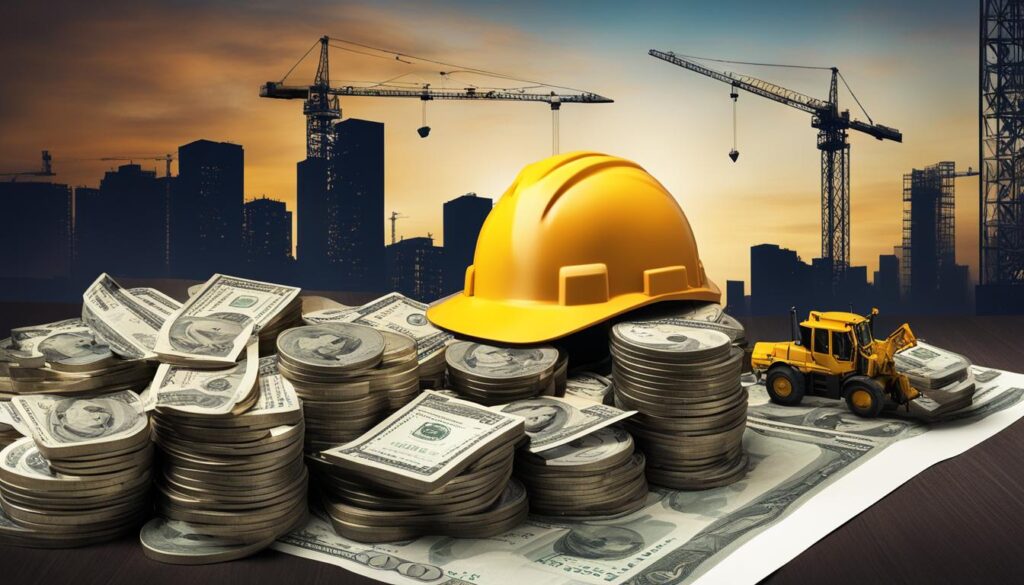
“It is common for construction projects to involve loans, whether from banks, credit unions, or other financial institutions.”
External Factors Influencing Construction Expenses
While construction expenses can vary depending on project size and scope, external factors such as market conditions, economic factors, and supply chain disruptions can significantly impact overall costs.
Market Conditions
Market conditions, such as supply and demand, can impact construction expenses by influencing material prices and labor availability. For example, during periods of high demand, material costs may increase, while labor shortages can drive up wages. On the other hand, a slow market can lead to lower costs as competition among suppliers and contractors increases.
Economic Factors
Economic fluctuations, including inflation, interest rates, and changes in GDP, can also impact construction costs. Rising interest rates can increase financing costs, while inflation can drive up the prices of materials, labor, and equipment. Economic downturns can also shrink the pool of available projects, leading to greater competition and lower prices.
Supply Chain Disruptions
Disruptions in supply chains, whether due to natural disasters, geopolitical instability, or other factors, can also impact construction expenses. For example, a shortage of raw materials can drive up prices, while delays in shipping or delivery can stall project timelines and increase labor costs.
Overall, external factors can have a significant impact on construction expenses, highlighting the importance of staying aware of market and economic trends and building contingency plans to mitigate the risks associated with supply chain disruptions.
Conclusion
In conclusion, the construction industry encompasses a wide range of expenses, with some being larger than others. We identified materials, labor, equipment, permits, overhead, design, financing, and external factors as significant contributors to the overall expense of construction projects.
Understanding the various components of construction costs is crucial in making informed financial decisions. From material procurement to equipment rentals and regulatory compliance, every aspect of construction involves a financial implication. Therefore, it’s important to work with skilled professionals who understand how to optimize each stage of the construction process to minimize costs.
As the construction industry continues to evolve, it’s becoming increasingly important to adopt innovative practices that streamline financial processes and optimize resources. By embracing new technologies and leveraging data-driven insights, construction companies can reduce costs, enhance efficiency, and maximize profitability.
At the end of the day, the key to success in construction lies in managing expenses effectively. By identifying the largest expense in construction and developing strategies to control it, companies can position themselves for long-term growth and success in an ever-changing, competitive landscape.
FAQ
What is the biggest expense in construction?
The biggest expense in construction varies depending on the project, but typically, labor costs tend to be the largest expense for most construction projects. The workforce required for construction projects, including skilled laborers and tradespeople, can significantly impact the overall expense.
What are construction costs?
Construction costs refer to the expenses involved in carrying out a construction project. These costs include various components such as labor, materials, equipment, permits, overhead, design, financing, and compliance expenses. Understanding construction costs is crucial for effective financial management in the industry.
How do material costs impact construction expenses?
Material costs play a significant role in construction expenses. The cost of materials used in construction projects can vary based on factors such as market conditions, availability, and quality. Material procurement decisions, including sourcing, pricing, and logistics, can significantly impact the overall expense of a construction project.
Why are labor costs important in construction?
Labor costs are crucial in construction because the workforce is the backbone of any construction project. Skilled laborers and tradespeople contribute to the construction process, and their wages, productivity, and availability can greatly influence overall project costs. Additionally, the industry is currently facing a shortage of skilled labor, which can further impact labor expenses.
What are the costs associated with equipment and machinery in construction?
Construction projects often require the use of equipment and machinery, and these costs can be significant. Expenses can include purchasing or renting equipment, maintenance and repair costs, fuel, and operator wages. Technological advancements in equipment can also impact expenses as newer and more efficient machinery is introduced.
How do permits, inspections, and compliance impact construction expenses?
Permits, inspections, and compliance requirements are essential in construction and can contribute to expenses. Obtaining permits and complying with regulations often entail fees and additional documentation. Inspections are necessary to ensure safety and quality standards are met, and failure to comply with regulations can result in penalties or delays, which can further impact project costs.
What are overhead and administrative costs in construction?
Overhead and administrative costs in construction include expenses associated with project management, office operations, insurance, and other administrative functions. These costs are necessary for the smooth operation of construction projects and can contribute to the overall expense.
What do design and architectural expenses in construction involve?
Design and architectural expenses in construction involve costs related to hiring design professionals, creating construction drawings, and engaging consultants. These expenses ensure that the project meets aesthetic and functional requirements, and they are important for achieving the desired outcome and quality of the construction project.
How do financing and interest costs impact construction expenses?
Financing and interest costs are an integral part of construction expenses. Construction projects often require financing through loans or other means, and interest expenses and loan fees contribute to the overall project cost. Understanding the financial aspects of construction and managing financing can help mitigate expenses.
What external factors can influence construction expenses?
Construction expenses can be influenced by various external factors. Market conditions, such as fluctuations in material prices, labor availability, and economic factors, can impact project costs. Additionally, supply chain disruptions, such as delays in material deliveries or availability, can also affect construction expenses.